Sanitary and Safety Attributes Help Dorner earn BISSC Certification on its Redesigned AquaGard 7350 V2 Sanitary Conveyor Platform
Launched in October 2018, the redesigned AquaGard 7350 V2 Series merges the best qualities in accessibility and safety to deliver a sanitary platform that’s perfectly engineered for the baking, snack food, pharmaceutical, pet food and packaging industries that require wipe-down and occasional wash-down cleanings of the conveyor.
HARTLAND, Wis., (May 16, 2019) — The high sanitary and safety attributes of Dorner's newly redesigned AquaGard 7350 V2 Series has earned it the coveted Baking Industry Sanitation Standards Committee (BISSC) certification for conveyors outlined in ANSI/ASB/Z50.2-2015. BISSC certification is recognized as the definitive sanitation standard for equipment used in the baking industry.
Specific design features that helped the AquaGard 7350 V2 earn BISSC certification include:
• Bolt-together 304 stainless steel frames
• FDA-approved belting and plastic components
• Open design with minimal horizontal surfaces
• Ample access for cleaning and maintenance
• Suitable for both wipe-down and low-pressure washdown cleanings with non-caustic solutions
Additional sanitary and safety features on the modular belt curve conveyor include having no openings greater than the international standard of 4mm, which increases safety by eliminating pinch points for operators. Furthermore, the upper and lower chain edges are fully contained in the drive system to reduce catenary belt sag and conveyor noise.
BISSC is a not-for-profit corporation that, working with the American Society of Baking Z50 Committee, developed an American National Standards Institute (ANSI) standard for the design of bakery equipment. The standard provides guidance for a variety of manufacturing equipment regarding proper design for sanitation and food safety.
For more information on Dorner's AquaGard 7350 V2 sanitary conveyor platform earning BISSC certification, visit www.dornerconveyors.com.
Connect with Dorner on Facebook at www.facebook.com/dornerconveyors
Follow Dorner on Twitter at www.twitter.com/dornerconveyors
Subscribe to Dorner on YouTube at https://www.youtube.com/user/DornerConveyors
Follow Dorner on LinkedIn at www.linkedin.com/company/dorner-mfg-corp
###
Hartland, Wisconsin-based Dorner is a world leader in the design, manufacture and distribution of high-quality conveyors and related equipment. Since 1966, companies from around the world have turned to Dorner conveyors for greatly improved efficiency and productivity. For more information about products or company news, visit Dorner's Web site at www.dornerconveyors.com or call 1-800-397-8664.
Featured Product
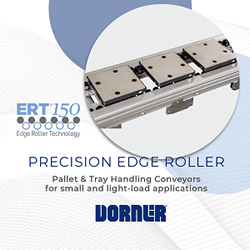